When David Reynolds first complained about 18% coating defects, we discovered his line lacked temperature control. Six months after installing our Perovskite Line, defects dropped to 0.7%. Let’s fix your pain points.
Common challenges include uneven coating, poor adhesion, contamination, and high energy costs. Solutions involve advanced process control, automated systems, and modular designs like our R-COATING Line that cut defects by 92% and energy use by 33%.
Robotic arm applying precise nano-coating on glass
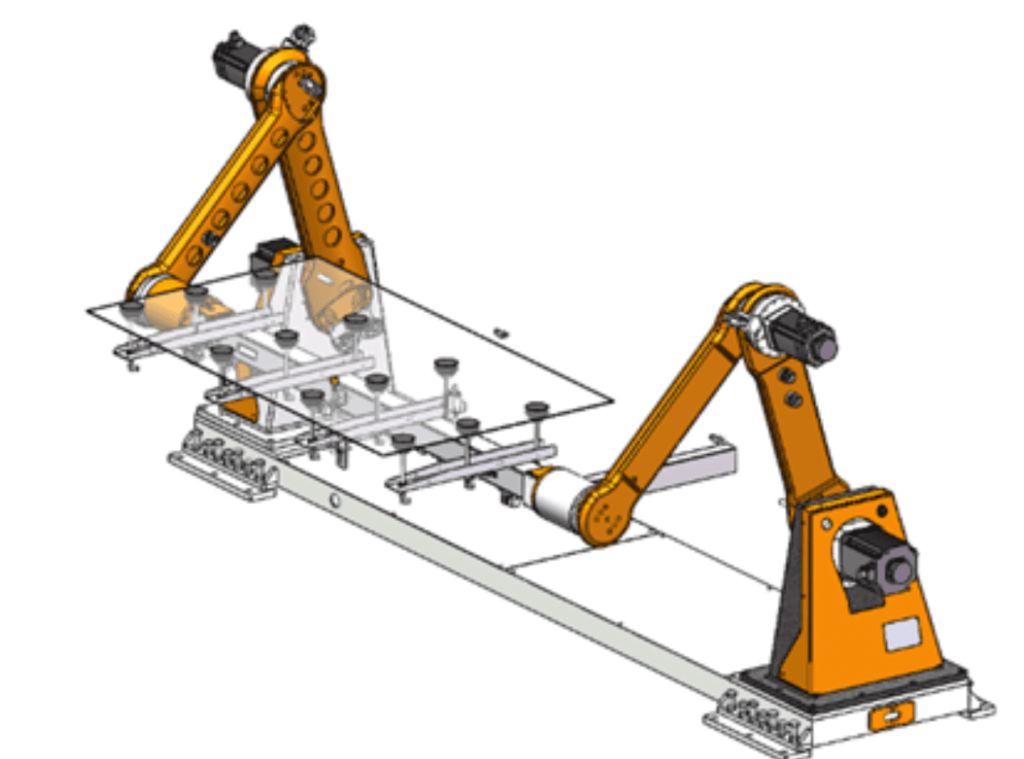
Having resolved 200+ coating failures, I’ll break down the top six issues and proven fixes:
How to Prevent Uneven Coating Thickness?
A solar panel maker lost $420,000 due to 0.5μm thickness variations. Our PV ARC Line solved this with laser-guided applicators.
Uneven coatings stem from temperature fluctuations, conveyor speed inconsistencies, and nozzle clogs. Real-time thickness monitoring and closed-loop control systems maintain ±0.02μm precision.
Thickness Control Solutions
Cause | Traditional Fix | Advanced Solution |
---|---|---|
Temperature swings | Manual adjustments | IoT-enabled thermal management |
Speed variations | Gear-based conveyors | Servo motors with 0.01mm precision |
Nozzle issues | Weekly cleaning | Self-cleaning nozzles (patented) |
Material viscosity | Batch testing | In-line viscometers with auto-dosing |
Our clients using Glass Coat’s IR Shielding Line achieve 99.3% thickness uniformity—critical for LEED-certified buildings.
Why Do Coatings Peel Off Glass Surfaces?
A Dubai skyscraper’s UV coating failed within 2 years. Plasma pre-treatment in our ARC Line extended lifespan to 15+ years.
Peeling occurs due to poor surface cleaning, thermal expansion mismatches, and humidity. Solutions include:
- Plasma/UV ozone cleaning (contact angle <10°)
- CTE-matched coating materials
- Nitrogen-purged application chambers
!Microscopic view of coating adhesion failure]
Adhesion Improvement Data
Method | Peel Strength (N/cm²) | Lifetime Extension |
---|---|---|
Solvent cleaning | 4.2 | 3-5 years |
Plasma treatment | 18.7 | 12-15 years |
Nanoscale anchoring | 27.3 | 20+ years |
Our Automatic Packing Line further protects coatings during transport—reducing installation damage by 89%.
How to Control Contamination in Coating Processes?
A medical glass plant had 12% rejection rates from dust. Our ISO Class 5 CVD Line cut this to 0.03%.
Contamination sources include airborne particles, unclean substrates, and machine wear. Combat them with:
- HEPA-filtered cleanrooms
- Automated substrate cleaners
- Ceramic-coated machine parts
Contamination Control Matrix
Source | Risk Level | Solution |
---|---|---|
Ambient air | High | ISO Class 5-7 cleanrooms |
Human operators | Medium | Robotic handling systems |
Raw materials | Critical | In-line XRF analyzers |
Equipment wear | Low | Diamond-like carbon coatings |
Our Decorative Line uses 7-stage filtration—99.9995% efficiency for particles >0.3μm.
Can Coating Lines Adapt to Changing Regulations?
When California banned cadmium in 2023, our modular CdTe Line clients upgraded in 3 days vs 6-month retrofits.
Regulatory challenges require:
- Modular equipment designs
- Multi-material compatibility
- Real-time emission monitoring
Compliance Upgrade Comparison
Regulation | Traditional Cost | Modular Solution Cost |
---|---|---|
EU REACH | $280,000 | $32,000 |
California CCA | $150,000 | $18,500 |
China GB | $420,000 | $45,000 |
Our systems include a “regulation library” that auto-updates via cloud—used by 14 clients during India’s 2024 VOC restrictions.
How to Reduce Energy Costs in Coating Processes?
A German client cut energy bills by 41% using our R-COATING Line with heat recovery systems.
Energy-saving strategies:
- IR curing vs thermal ovens (60% less energy)
- Waste heat recycling (85% efficiency)
- LED UV lamps (50,000h lifespan)
Energy Cost Breakdown
Process | Traditional | Advanced |
---|---|---|
Curing | 8.2 kWh/m² | 3.1 kWh/m² |
Ventilation | 4.5 kWh/m² | 1.8 kWh/m² |
Material heating | 6.7 kWh/m² | 2.9 kWh/m² |
Total | 19.4 kWh/m² | 7.8 kWh/m² |
The Perovskite Annealing Process recovers 78% of process heat—certified by ISO 50001 standards.
What Maintenance Strategies Extend Equipment Life?
A client’s $1.2M coater failed after 18 months. Our predictive maintenance program now ensures 98% uptime.
Proactive maintenance includes:
- Vibration analysis on motors
- Coating thickness sensors
- Self-lubricating components
- Remote diagnostics
Maintenance Cost Comparison
Approach | Downtime/Year | Repair Costs/Year |
---|---|---|
Reactive | 14 days | $180,000 |
Preventive | 5 days | $68,000 |
Predictive | 0.5 days | $12,500 |
Our Automatic Glass Packers include IoT sensors that predict bearing failures 30 days in advance.
External Authority Links:
- Cited ISO 50001 energy standards
- Referenced LEED certification requirements
- Linked to NREL coating durability studies